Lifeline for Robots
The robots take 57 seconds to build a door for the new BMW X1. They should do this fault free for up to seven years. This is hard work even for the robotic tool’s energy supply systems from HELUKABEL subsidiary Robotec Systems.
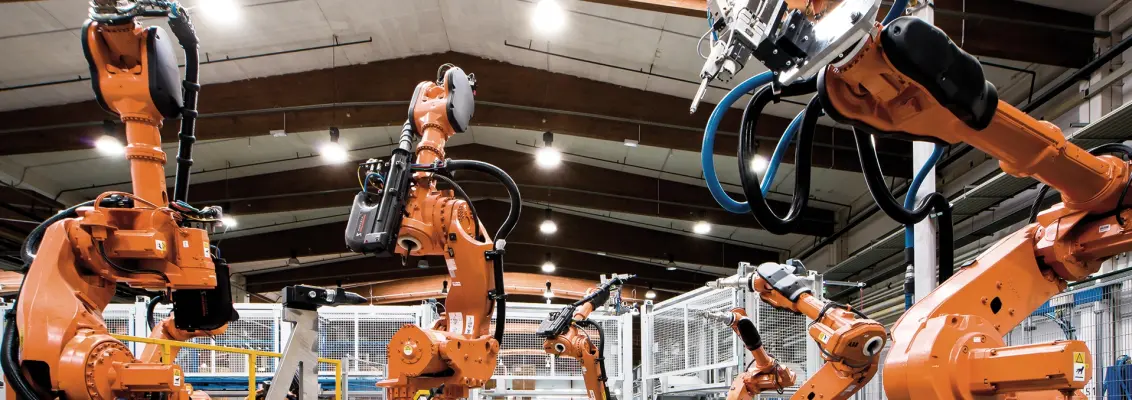
Near Regensburg, in the Bavarian town of Elsendorf, a state-of-the-art plant is being created to produce the doors for the new BMW X1. “We at BMW are taking charge initially. As a service provider, we design the plant, select the supplier, and completely construct the plant. If everything works, we hand it over to the owner, in this case it’s our supplier Magna,” reports Manfred Scheuerer, who is responsible for production planning at BMW. “Through this so-called third-party business, we set production and quality standards worldwide,” he adds. As is the norm in automotive construction, most of the work is performed by robots, even door production. There are 76 high-volume robots in the massive facility, distributed across four plants for the production of the two front and rear doors. In a three-shift operation, they put together around 700,000 doors per year from sheet metal parts produced by Magna in Graz using a spot welding gun and a glue gun.
ONE MILLION TORSION CYCLES
The plant should run fault free for up to seven years. As the robots are essentially offered without tools, they need a supply system, i.e. the power, cooling water, data and adhesive must be fed to the tool head by cables and hoses. In addition to the standardised technical specifications of the cables and hoses for the respective tools, BMW also defines qualitative requirements. These are saved as formulae in the requirement specification and calculated from the maximum tolerated downtime of the plant. “The load on the cables and hose packages is dependent on the movement radii of the robotic arms. Additionally, with all the movements in the case of welding robots, the burn off cannot be prevented from getting between the cables and hoses and acting like sandpaper. This considerably increases the wear and may shorten the lifetime. However, in our internal quality control, all products must withstand one million torsion cycles. This is made possible because of the structure and material composition of the cables used from HELUKABEL. As such, we ensure that our systems withstand even the high demands of BMW,” explains Volker Elbe, sales manager at Robotec Systems.
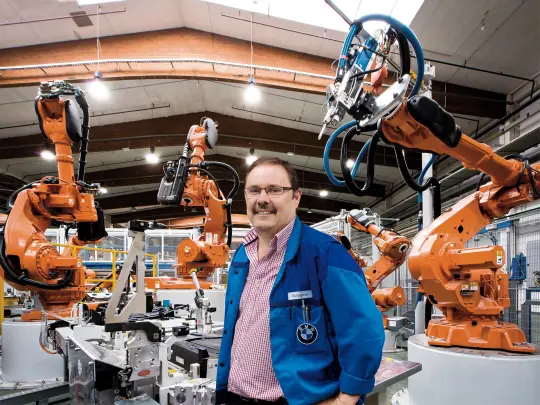
PLACING THE STRAIN ON THE ROBOT
In production planning, overcapacity should be avoided. The plant size and design are therefore simulated in advance using production planning software. “Starting from annual output and cycle time, we calculate the performance data for each individual robot. To do this, we need simulation data for all of the parts that the robot has to move. This is the only way that we can design the robot performance exactly for the actual requirements,” explains Scheuerer. “The load is the sum of all the parts that the robot has to move in the defined cycle time. Furthermore, the tools, handling, work piece itself, and the energy supply system for the tools must be taken into account,” he adds. The simulation data includes not only weight data but also the exact location of the centre of gravity. “Our aim is to design all robots for 90 percent capacity use. That puts us on the safe side in respect to the seven-year lifetime of the plant,” says the BMW planner. “Providing the load data for BMW was a challenge for us within the project,” Elbe reports. Robotec Systems established itself as a supplier to BMW through a tendering process. “However, we had to settle the mathematical load data issue beforehand. After all, with the cables and hoses sitting like a rucksack on the robot arm, a field pack of over 40 kg (90 lbs) is amassed. Today, we are able to supply load data and 3D simulation data for all our systems. Through this project, we have been able to expand our experience so future customers also benefit from it,” says Elbe, expressing his pleasure. In autumn 2013, BMW ordered the first 30 systems for handling, gluing and spot welding robots. These were supplied and assembled by Robotec Systems in around six weeks. All the robots are now fitted and BMW planner Manfred Scheuerer is at the point of handing over the Magna plant. Production should then begin in February 2015.
BRINGING ROBOTS TO LIFE
Automotive and high-volume robots from all manufacturers need a supply system for the respective tools. Besides power, cooling water, compressed air or transport tubes for rivets, screws and adhesive, there are also high-performance data cables for the tool heads. Robotec Systems specialises in the development and production of such energy supply systems.