Joint Effort
The second generation of Sumitomo (SHI) Demag’s fully electric IntElect injection moulding machines combines long-standing know-how with the cable expertise of HELUKABEL’s sales representative, Uwe Wohner.
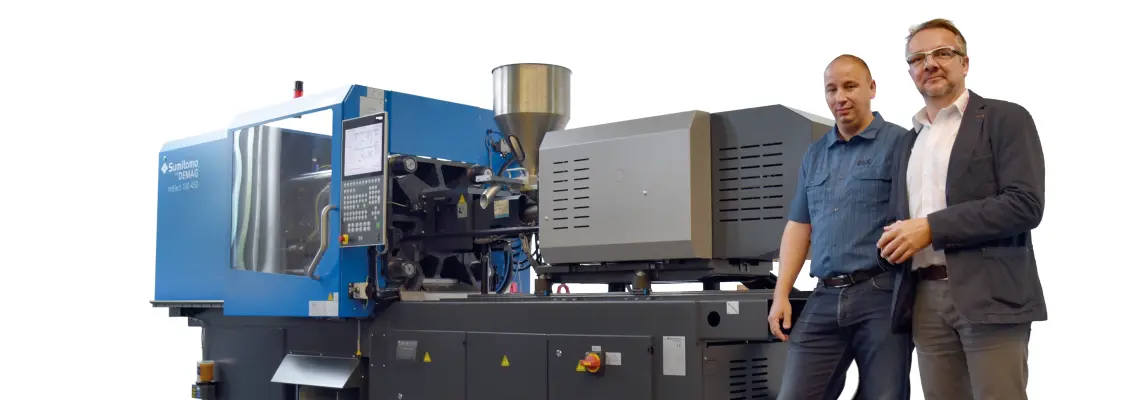
At an in-house trade fair hosted by Sumitomo (SHI) Demag last May, the 500 or so invited guests are very impressed by the 50-tonne IntElect 50 injection moulding machine before them. The fully electric injection moulding machine series is equipped with special high-torque direct drives that provide maximum precision and dynamic performance. The IntElect 450, previously the largest injection moulding machine available, is an integral part of a highly efficient electric production cell that manufactures polycarbonate headlight covers for the automotive industry. The machine can be operated as intuitively and easily as a smartphone, thanks to the NC5 plus control system, which has a colour touch screen with a glass surface.
STRONG PARTNERS
This development has been made possible thanks to the know-how acquired by the Sumitomo Group over decades in the field of electric drives. More than 65,000 of the company’s fully electric machines are in operation throughout the world. The consistent alignment with customer requirements has contributed to their widespread use. “After the trade fair, we more or less completely reworked the prototype,” reports Marc Spenner, Sumitomo’s series design engineer in Wiehe. When it comes to making sure the cables also meet machine requirements, he relies on the expertise of HELUKABEL’s sales representative, Uwe Wohner. “About 90 percent of the machine’s cables are from HELUKABEL. Some of them are exposed to great stresses which means they must have certain qualities. We also find his advice invaluable when it comes to using UL-style cables in machines for the export market,” explains Spenner.
FLEXIBLE | OIL-PROOF |
Injection moulding machines from Sumitomo (SHI) Demag are designed for use in series production and multishift operations, such as the automotive industry. HELUKABEL’s special drag chain cable, the MULTIFLEX 512-PUR, is ideal for this type of application. | Even electric machinery cannot completely avoid using oil- operated hydraulic power units for certain processing steps, so it is important that cables in injection moulding machines be oil-proof. Common oils, greases, and lubricating coolants do not damage the highly flexible “I-BUS Drag Chain” BUS cable. |
SCREENED | INTERNATIONAL |
In fully electrical-operated machinery, perfect screening is essential for the secure transmission of signals and feedback. The rounded TUBEFLEX-(ST)-CY ribbon cable is double-screened for reliable protection against electrical interference. | Sumitomo (SHI) Demag produces the IntElect series in Germany for the international market. The cabling must comply with the respective regulations and standards. MULTINORM control cables such as the HELUKABEL JZ-603-CY are approved in many countries, which simplifies the export process. |
THE PLASTIC EXPERTS
Who: Sumitomo (SHI) Demag Plastics Machinery GmbH, Schwaig and Wiehe, 3,000+ employees.
What: The injection moulding machine specialist for plastics processing is a global leader in this sector along with its Japanese parent company Sumitomo Heavy Industries.
THE CABLE EXPERT
Uwe Wohner is area sales manager for Thuringia. He has been attending the needs of the Sumitomo (SHI) Demag subsidiary since 2008. The subsidiary in Schwaig has been a HELUKABEL customer since 1996. Uwe Wohner’s valuable advice is especially sought after when it comes to the tricky task of finding the right cable for the export market.